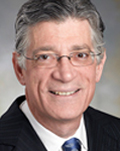
Summer 2016 - Vol. 11, No. 2
Drug Shortages: A Persistent Problem
Randall A. Oyer, M.D.
LGHP — Hematology and Medical Oncology
Ryan Breznak, R.Ph.
Lancaster General Hospital
INTRODUCTION
The term “drug shortage” is used to indicate a change in the drug supply that has the potential to compromise patient care. Drug shortages are a challenge for physicians and hospitals, as they typically appear with little or no warning, and significant resources may be needed to manage patients when a particular therapy is unavailable or in short supply.
1
Changes in the drug supply can affect the way medications are prepared in the pharmacy, the way they are administered to patients, and, in some cases, whether patients receive medications at all. When faced with any drug shortage, the ultimate goal is to avoid the inability to treat a patient with effective medication.
Nationwide, there are currently 154 medications unavailable or in short supply; 138 are total product outages (all concentrations or sizes), and 16 are experiencing specific shortages in certain concentrations or sizes. Additionally, there are approximately 20 intermittent shortages.
2
As a general principle, lower cost, generic, multisource products experience shortage issues more often than brand name specialty products. Shortages that reach the hospital and affect patient care are often of prolonged duration and may last many months.
WHY DRUG SHORTAGES OCCUR
The process of delivering medications to patients involves multiple steps — from obtaining raw materials, to manufacture, distribution, and delivery. Some of the factors influencing drug supply may be predictable; many are not. At Lancaster General, drug shortages have been encountered over the past two years due to a variety of factors.
Unpredictable Factors:
• Raw material shortages. The majority of raw materials used in pharmaceutical manufacture come from outside of the United States. Natural disasters may affect the availability of source plant material or may damage overseas processing facilities, which can be especially important when there is only one source of raw materials.
• Manufacturing difficulties due to regulatory issues. Shortages may occur when a primary or sole manufacturer of a product has its production halted by the Food and Drug Administration (FDA) for breach of good manufacturing practices (GMPs).
• Voluntary product recalls. These may occur due to a range of internal problems within a manufacturing facility or supply chain, creating shortages that may be especially acute when one manufacturer supplies the majority of a given product.
Predictable Factors:
• Increases in demand due to shifts in clinical practice. Expanded labeled uses, disease outbreak and updated clinical guidelines can increase utilization of a single pharmaceutical product.
• Market shifts. The addition of a generic product to the market may sometimes precipitate a prompt decrease in manufacture of the brand-name original product, creating a temporary reduction in the overall supply until the generic manufacturer ramps up production.
• Depleted wholesaler /distributer stocks. This is increasingly common because both wholesalers and health systems maintain minimum levels of stock and utilize “just in time” inventory practices that can lead to mismatch of supply and demand at the wholesale level.
• Manufacturer discontinuation. A manufacturer may stop production of a drug because of inadequate financial return, poor demand, or potential safety concerns.
• Industry consolidations. Mergers between manufacturers may result in decisions to refocus product lines and discontinue certain products.
• Anticipatory buying. Anticipated price increases may lead to stockpiling, which creates artificial shortages. This can be intentional, leading to “gray market” resale of products back to users at inflated prices.
THE EXPERIENCE AT LGH
The LGH pharmacy currently has approximately 50 different items (2% of all line items) that require close monitoring on a daily basis because of supply uncertainties. There are 8 product categories of top concern (Table 1).
What we monitor in the LG Department of Pharmacy on a daily basis:
• Shortages identified or anticipated in the market
• Manufacturer and distributor allocations
• Unfilled backorders
• System-wide inventory and expiration dates
• Quality and cost of products in the marketplace
• Resolution of known or anticipated product shortages
There may be no advance warning that a shortage may occur as the pharmaceutical industry is not required to communicate about the availability of products. However, pharmaceutical companies are required to notify the FDA when a sole manufacturer plans to discontinue production of a medication, or if manufacturing interruptions or production changes could disrupt supply.
A drug shortage may first be brought to our attention by pharmaceutical representatives or other industry peers. Additionally, we routinely monitor the website of the American Society of Health-System Pharmacists (ASHP) for its list of drug shortages. Occasionally we only become aware of a drug shortage when we are unable to order or obtain a medication from its supplier or distributor.
In accordance with the LG Department of Pharmacy Services Policy,3 when a drug shortage is identified we validate the details of the shortage by contacting the manufacturer, we obtain as much information as possible to estimate the time until the shortage impacts us, and we assess any opportunity to obtain an allocation. Pharmacy staff determine if an alternate product presentation is available, if an alternative can be formulated in the pharmacy, or if there is a therapeutic substitute. This information is communicated across the pharmacy and to ordering physicians.
Additionally, we carefully analyze the operational, financial, and clinical impact. Physicians may occasionally be called upon to develop criteria for allocating a product in short supply for use in high-risk patients for a specific indication. When a shortage is in effect, pharmaceutical cost is likely to go up and considerable time is spent on assessment, analysis, communication, and implementation. Additionally, risk management and legal representatives must be notified when all options for obtaining either drug product or acceptable alternatives have been exhausted.
What is happening outside Lancaster General
All U.S. hospitals are impacted by drugs shortages and most have developed long and short-term strategies for managing them that include strategies for conservation, stockpiling, and /or changing practice. Statements and guidance on managing drug product shortages in hospitals and health systems have been issued by many professional organizations, including the AHSP, the Association of Community Cancer Centers (ACCC), the University of Utah Drug Information Service, and others.
One of the most unfortunate outcomes of this problem is the development of a gray market. Nontraditional distributors (also known as open market, gray market, or alternative distributors) are licensed distributors or brokers who obtain products in short supply for the purpose of reselling them to end users who are unable to obtain them through normal suppliers. These distributors aggressively market the availability of their products, often in limited quantity. Unlike traditional distributors, the gray market does not guarantee a product’s pedigree or ensure the reliability of its source, nor is their assurance of proper handling and storage throughout the chain of custody. Additionally, compounding pharmacies have pursued the production of drugs that are in short supply. Caution is warranted here as well, because preparations from compounding pharmacies may not meet applicable state or Federal standards and the sources of raw materials used by compounding pharmacies may not be verifiable.
In cancer medicine, one of the most respected sources of guidelines is the National Comprehensive Cancer Network (NCCN).4 Their guidelines for colon cancer treatment include guidance about a substitute for calcium leucovorin, which has been in short supply for years. The AHSP also provides therapeutic alternatives for drugs in shortage,5 but the FDA does not provide therapeutic alternatives because doing so falls within the practice of medicine.
CALL TO ACTION
How can you help? Write a letter to the FDA at drugshortages@fda.hhs.gov
The Food and Drug Administration cannot require a pharmaceutical company to make a drug, increase its supply, or influence its distribution. However, it can improve its oversight of drug shortages.
Ask the FDA to require that manufacturers provide a central contact point for shortages. Require the company to quantify the duration of the shortage in days, weeks, or months. Require six months’ notice of any discontinuation or planned interruption in production.
S. 296 (112th): Preserving Access to Life-Saving Medications Act, a bill to give the FDA improved capacity to prevent drug shortages, was introduced by Senator Amy Klobuchar (D Minn) on February 7, 2011 and died in Congress.
REFERENCES
1. Manual of Policies and Procedures Center for Drug Evaluation and Research. "Drug shortage Management.” Pp 1-24. MAPP 4190.1 Rev 2 9/3/2014
2. Drug Shortages Infographic, U.S. Food and Drug Administration. http://www.fda.gov/Drugs/DrugSafety/DrugShortages/ucm441579.htm 3/28/2016
3. Lancaster General Health Department of Pharmacy Services Policy and Procedures Manual. Policy #3106. Title: Notification for critical drug shortages. Effective: 01/2015.
4. National Comprehensive Cancer Network (NCCN) Colorectal Cancer Guidelines. V 2.2016; COL-C 6 of 9
5. McBride A. National Survey on the Effect of Oncology Drugs Shortages on Cancer Care. Am J Health-Syst Pharm. 2013; 70: 609-611.